We impregnate wood with Burnblock® fire retardant using the vacuum-pressure method in an autoclave, thanks to specially developed programmes and advanced technology, ensuring 100% non-toxic, heavy metal-free fire retardant treatment.
Wood that we have made fire retardant meets the highest possible fire safety standards and guarantees full environmental transparency, giving architects and designers a wide range of design solutions with full safety in all the above respects..
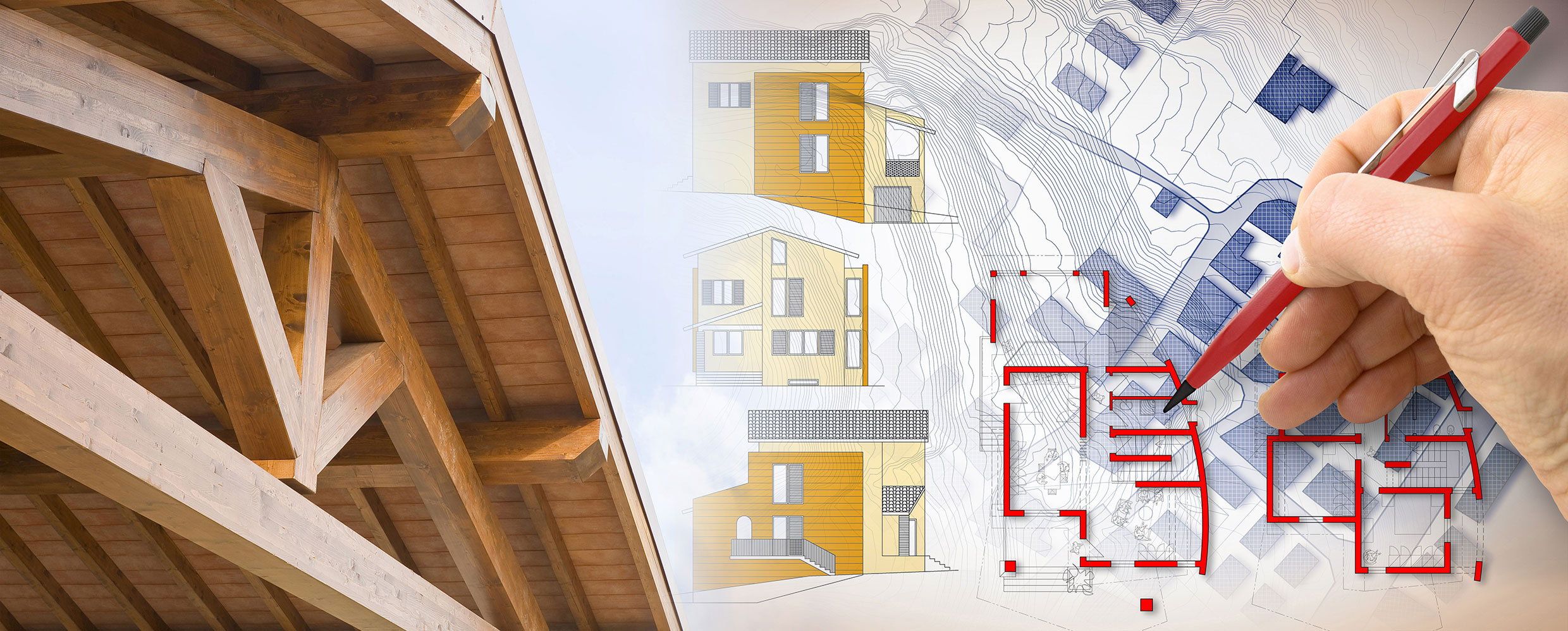
After fire retardant impregnation, wood retains its natural beauty and aesthetic qualities.
Burnblock® fire retardant provides effective fire protection for wood without having a negative impact on the environment. The combination of these two issues is crucial for society as a whole. The natural, 100% non-toxic fire retardant impregnation we offer guarantees that your investment projects will achieve the highest possible European classification in terms of reaction to fire: B-s1, d0 according to EN 1350-1, while meeting the Polish NRO standard
The innovative fire retardant wood process can be used for cladding and exterior facade treatment.
We achieve Euroclass B-s1, d0 for wood and wood-like products in an environmentally friendly way. The carbon footprint of Burnblock® treated timber is lower than, for example, composite products.
In this way, we combine innovative fire protection solutions with the sustainable use of wood.
We offer P-certified products and fire retardant impregnation services using the deep method in an autoclave.
The P marking is essential
The P marking is essential
Fire safety effectiveness that is not backed up by reliable testing, documentation and certification for a fire retardant product has little international value. It is therefore a priority for us and Burnblock Aps to obtain numerous certifications and environmental declarations.
We would like to introduce you to one of the most common and important certifications for European companies – the P marking.
The P marking is a key indicator of a product’s compliance with the legal requirements of the European Union, allowing it to be sold in the European Economic Area and Turkey, among others. It means that the product has passed the manufacturer’s tests and has been found to comply with EU health, safety and environmental requirements. The P marking is mandatory and must be affixed to the product before it is placed on the market.
FIRE CLASSIFICATION IS NOT ALL!
Fire classification is just a classification report of the fire test carried out on the material in question.
The fire classification as a document according to EN 13501-1 Bfl-s1 or B-s1, d0 does not constitute a European or national technical assessment or a PRODUCT CERTIFICATE.
The requirement for the P marking covers various product groups, including products in the construction and woodworking industries that are subject to EU specifications and regulations.
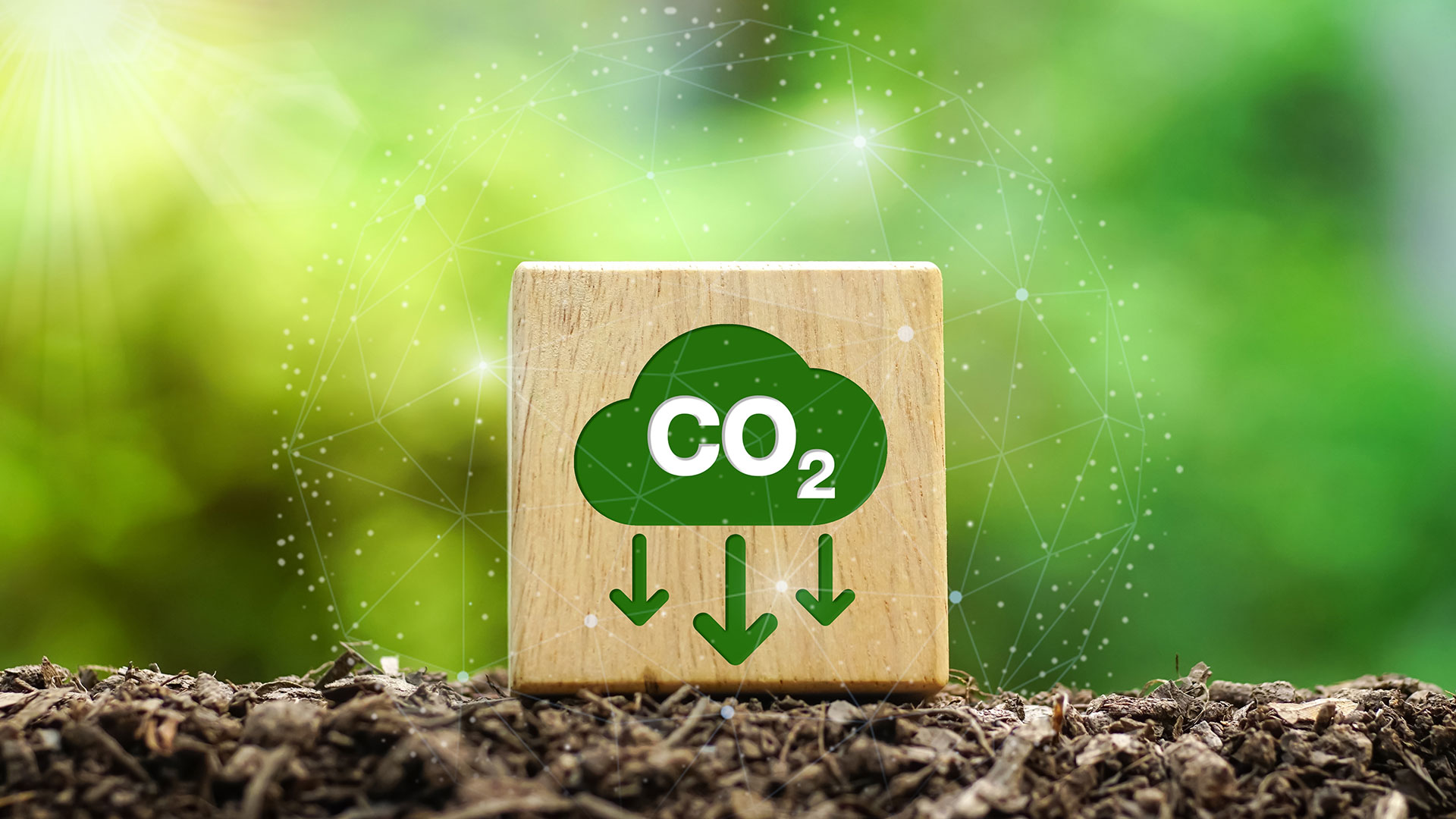
The P marking of a product is also linked to AVCP. The Assessment and Verification of Constancy of Performance is a harmonised system that defines how products are assessed. It is applicable in Europe, particularly in the areas of protection of human life. Work with fire anywhere is subject to the AVCP procedure at level 1/1+.
The levels indicate the degree of protection. Certification to levels 4, 3, 2 is fairly straightforward, while certification to levels 1 and 1+ requires an external audit by a notified body. This is a key element of the P marking process for construction products, so all processes must comply with the P requirements.
The audit by the notified body makes it clear, for example, whether the wood or engineered wood that is subject to the verification system is the same wood or engineered wood that the customer receives. The results of the assessment and the factory production process control make it possible to verify that the performance parameters do not change over time. The AVCP system verifies the procedures that manufacturers must follow to declare the performance of each relevant component, such as test methods, tabulated values, etc. Manufacturers are required to apply these procedures to the testing of samples and also to define the detailed factory production control.